3D Implant Manufacturing Process
There are four main steps in Tangible's 3D implant manufacturing process for orthopedic medical implants: discovery, prototyping, verification & validation, and alpha launch.

Discovery - 1 to 4 weeks
As partners, Tangible works closely with customers to gather specific product and process design requirements. Also discussed are:
- The manufacturability of a design and AM optimization
- The support strategy and manufacturability of the proposed design
- The driving requirements that need to be transferred if switching from another manufacturer
- Worst-case build requirements and any recurring printing artifacts
- Specific post-processing requirements
- Initial prototyping quotes
Prototyping - 1 to 4 weeks
Communication is key during prototype builds, and Tangible ensures each customer understands the design state and project delivery requirements. Tangible structures each prototype family to maximize effectiveness. Each build is thoroughly evaluated upon delivery. Through process refinement, the design will be locked down utilizing the advantages of additive‒the ability to adjust and re-design quickly. Process refinement helps ensure a more robust design for verification and validation, for 510k approval, and to keep costs down.
Verification & Validation - 6 to 8 weeks
Verification and validation testing includes mechanical testing, cleaning, packaging and sterilization. Depending on test type, parts may need to be worst case sizes, or may also be near net (unfinished) devices to save costs at this stage.
Alpha Launch - 8 to 12 weeks
Initial Production Run
Tangible can provide flexibility at this stage, building parts ahead for stock or holding for 510(k) decisions. Production lead times depend on product and scale, and can be planned up front so customer expectations are met.
Product development and 510(k) submissions are supported throughout the product manufacturing process. The Tangible team of experts, passionate about improving patient outcomes with superior service, is an extension of every customer’s organization, leveraging AM industry knowledge and experience to ensure the highest level of quality that exceeds expectations.
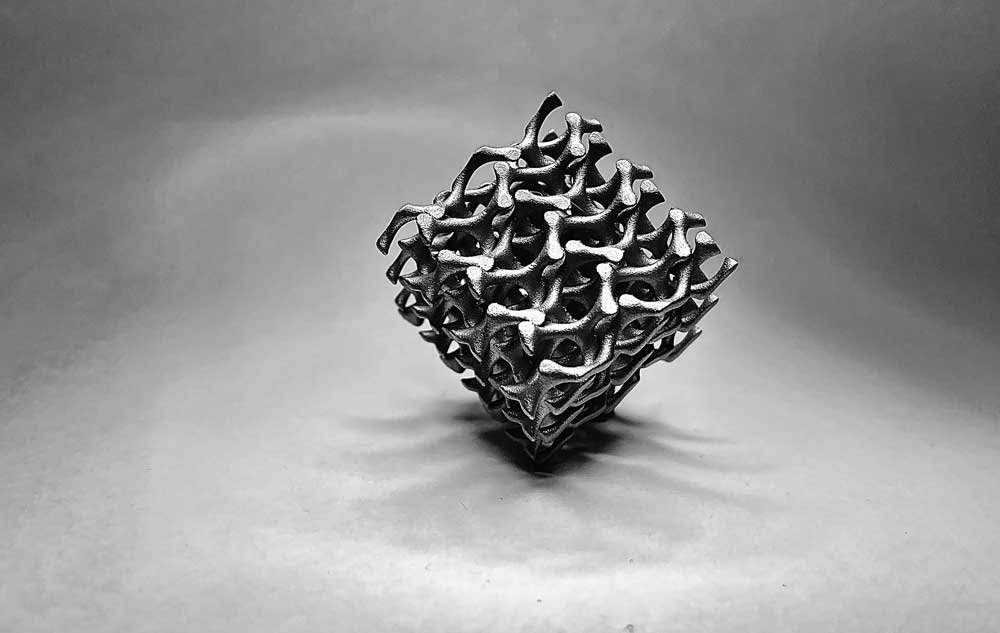
Ready to Get Started On Your 3D Printing Project?
Get your additive implants to market
Get Started TodayWhy Tangible Solutions
Professional Experience
Breadth of knowledge is gleaned from producing over one million orthopedic implants.
Industry Leader
Tangible Solutions has unparalleled expertise as a globally recognized contract manufacturer of American-made 3D printed titanium orthopedic implants.
Prototype to Monthly Orders
Continuous technological improvements driving innovation for developing powerful new medical devices quickly and cost effectively.
Technology Driven
Tangible engineering vision is mathematically driven, wielding the highly advanced power of nTopology, next-generation design software.